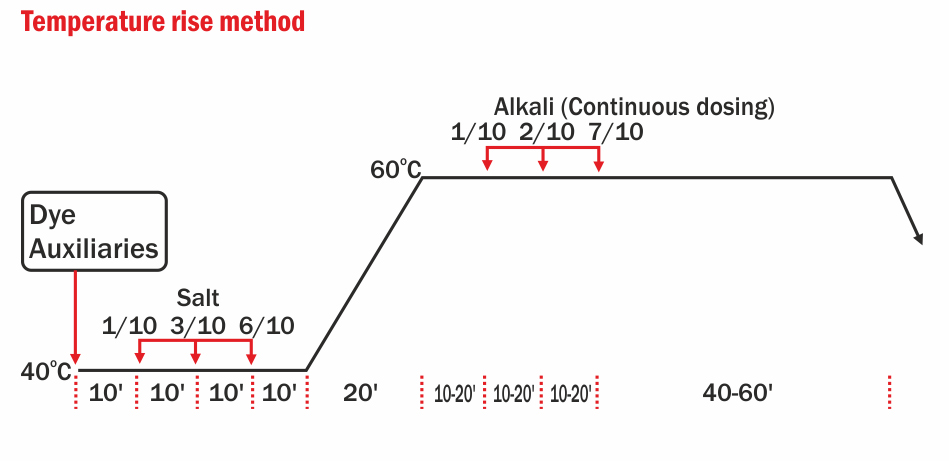
Depth of Shade % | Salt gms/lt. | Soda Ash (gms/lt.) |
Up to 0.5% | 30 | 10 |
0.5 to 1.0% | 40 | 15 |
1.0 to 2.0% | 50 | 15 |
2.0 to 4.0% | 50 | 20 |
Above 4.0% | 80 | 20 |
Washing & Soaping
After Dyeing it is necessary to remove the unfixed Dye to get a high level of wash fastness. It is also essential to remove the residual Salts and Alkali prior to soaping. The usual sequence is:
- Washing with cold water.
- Washing with hot water not above 60 °C.
- Soaping at boil for 15~30 minutes using 1-2 gm/lit of lissapol D.
- Rinsing with Warm Water at 50 °C.
- Rinsing with cold water, till squeeze water is clear.
Cold Pad-batch Dyeing
Dyes | X g/l |
Penetrating agent | 1-2 g/l |
Caustic soda | 5-35 g/l |
Sodium Silicate | 40-100 g/l |
Batching time | 6-24 hr. |
Continuous Dyeing
Padding Solution | |
Dyes | X g/l |
Urea | 0-50 g/l |
Reduction inhibitor | 10 g/l |
Migration inhibitor | 1 g/l |
Soda ash | 10-20 g/l |
Padding | |
Temperature | 20-25 oC |
Pick up | 60-80 % |
Drying | 110-120 oC |
Steaming | 102-105 oC, 60-90 sec. |
Printing
Sodium Alginate | ||
Depth | Upto 40 Parts Per 1 000 Parts | More than 40 Parts Per 1000 Parts |
Water | 150-200 | 200-250 |
Urea | 50-100 | 100 |
Resist Salt | 10 | 10 |
Sodium Bicarbonate | 15 | 30 |
Sodium Carbonate | 15 | 20 |
Bulk to | 1 000 Parts with Alginate Thickening & Water |
Process
Mix dye powder with urea and pour hot water of temperature about 80-85°C and stir well to dissolve completely. Add this dye solution to sodium alginate thickening paste containing resist salt stir well to mix. Just before printing add sodium bicarbonate.
Print the cloth with above print paste and dry. Avoid over-drying and protect printed goods from acid or reducing fumes. Then steam dried goods for 5-8 minutes on rapid ager or 15-20 minutes on star ager.